Guiding machines: Combining GNSS and other sensors is key to
Building a solid foundation for any construction requires that the ground be adequately compacted and leveled. Construction workers and contractors operating earthmoving machines know it is nearly impossible to do that by eyesight alone. For a few decades, leveling was accomplished using rotating lasers mounted on tall tripods, which could typically cover a little more than 1,500 ft on a job site and laser receivers mounted on masts on the earth-moving machines. However, these systems only provide elevation, not position, and must be repositioned frequently.
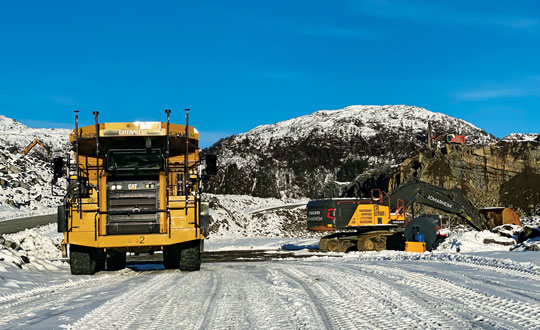
Photo: Steer
In recent years, laser leveling has been increasingly replaced by machine control systems that enable operators to compare the position of their machine’s blade with a digital grading map, and then guide it very precisely to cut the proper elevation. These machine control systems combine global navigation satellite system (GNSS) receivers, to provide the position of the machine; inertial navigation systems (INS), to bridge short gaps in GNSS availability and to provide the platform’s attitude (pitch, roll, and yaw); and a variety of other sensors, to determine the movement of the machine’s attachments, such as booms, arms and buckets.
In this month’s cover story, we feature perspectives on machine control from:
- Microchip, which makes inductive position sensors that monitor the angular and linear movements of the attachments.
- Septentrio, which makes the AntaRX series of smart antennas.
- Gundersen & Løken, which makes the DigPilot kit for excavators.
Besides grading, other areas for machine control include trenching at a specific depth, spot-bulldozing to better prepare a site for grading, mass excavation and contouring edges. Artificial intelligence (AI) will soon start taking over the operators’ duties, but that’s for a future article.